Shop Floor Connectivity Challenges
The lack of real-time visibility makes it difficult to monitor Line Efficiency (LE) and Overall Equipment Effectiveness (OEE). Additionally, existing systems do not have a direct communication interface between the top floor and the shop floor, leading to inefficiencies in data flow and decision-making.
Challenges
In manufacturing environments, achieving seamless connectivity between the shop floor and top floor is crucial for real-time monitoring and decision-making. However, several challenges hinder this process
Solution
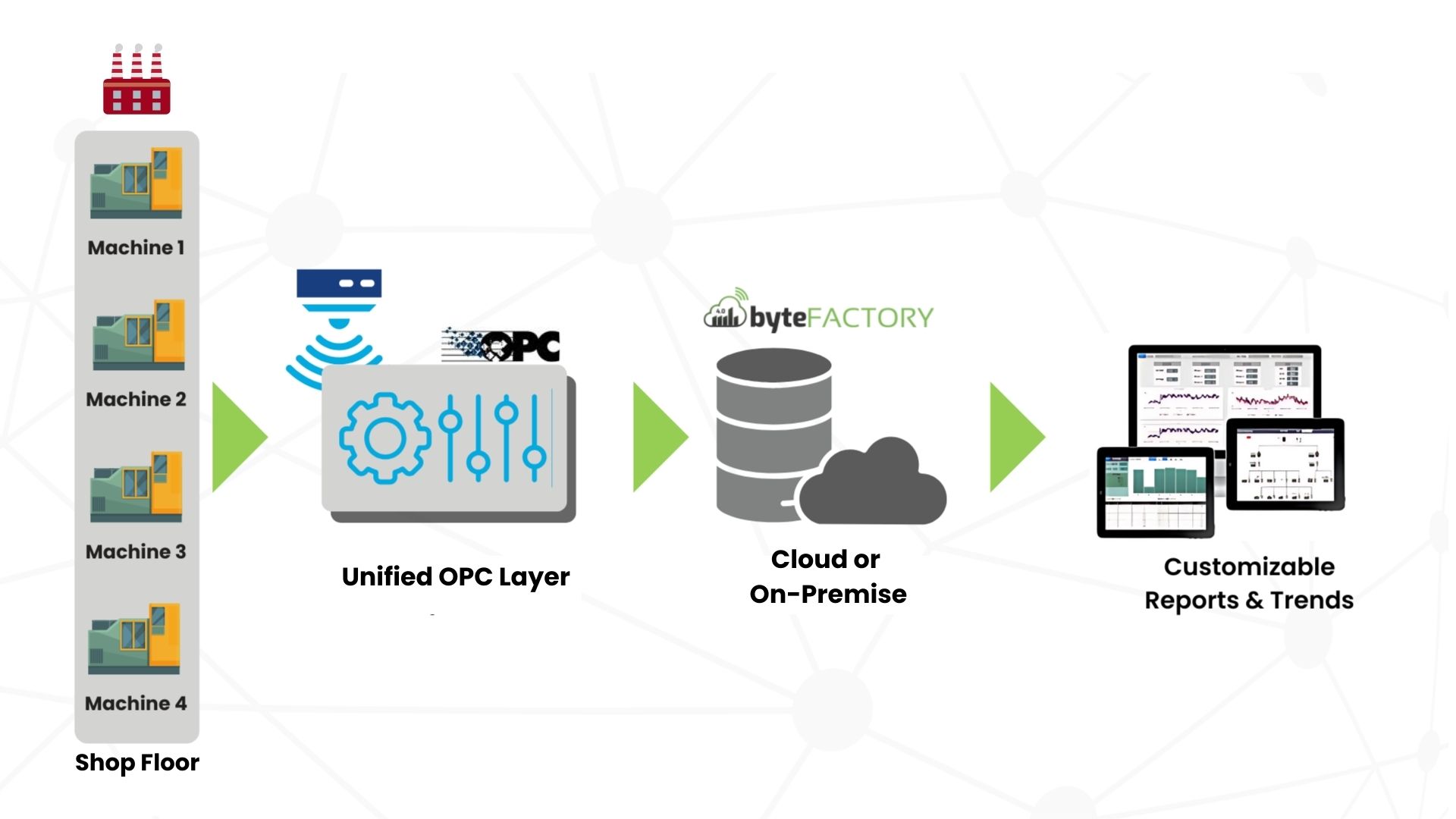
Machine & Device Integration – Machines and devices are connected to capture real-time production data at regular intervals from machine interfaces such as Programmable Logic Controllers (PLC).
Reliable Communication Interface – Ethernet or serial connections ensure seamless data transmission between machines and monitoring systems.
Data Acquisition & Processing – Kepware is used to read machine data by configuring PLC tag addresses for key operational parameters, ensuring accurate and timely data collection.
Deployed Technologies & Integration Approach
Sensors – Enable real-time industrial data collection for accurate monitoring.
DAQ System – Facilitates data acquisition and processing for actionable insights.
Edge Device – Performs localized computing & analysis, reducing latency and dependency on cloud processing.
Secured Cloud / On-Premises – Ensures safe and scalable data storage & access based on business needs.
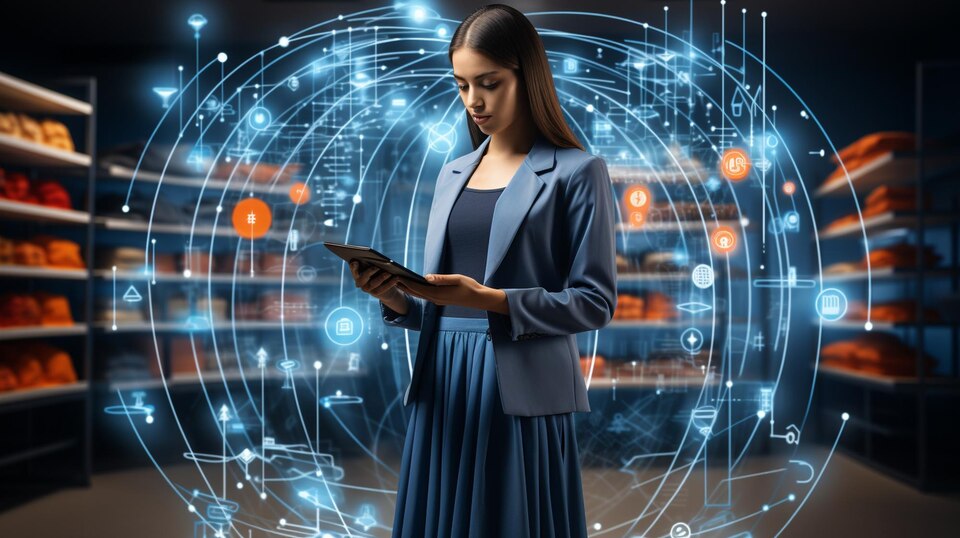
Tangible Results & Business Outcome
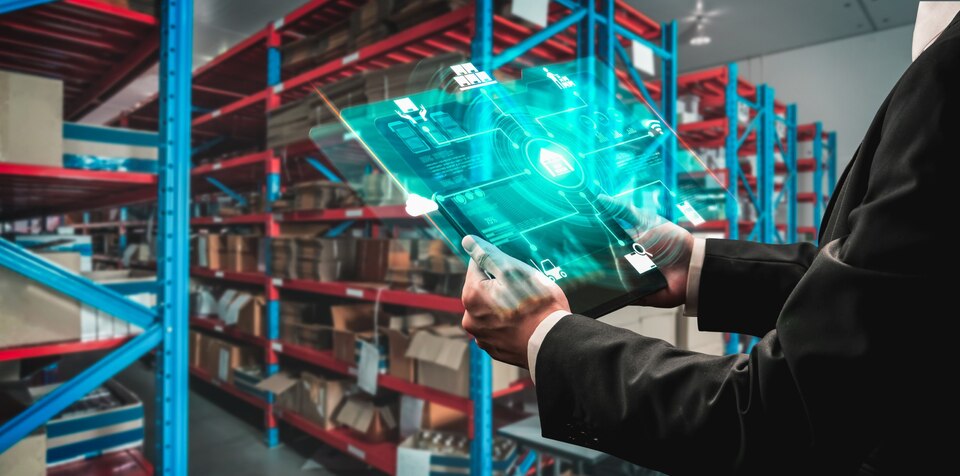
- 30% Reduction in Downtime: Real-time monitoring enabled early detection of system faults and minimized unplanned outages.
- 25% Faster Decision-Making: AI-driven analytics provided actionable insights, accelerating operational and strategic responses.
- Enhanced Mission Readiness: Pro-Active maintenance ensured critical systems were always combat-ready.
- Improved Asset Utilization: Centralized visibility across defence assets optimized deployment and minimized idle time.