AI-Powered Downtime Reduction Approach
Conventional maintenance strategies struggle with limited real-time visibility into machine health, making it difficult to monitor equipment efficiency and predict failures. Existing systems often lack integration between production floors and management, leading to delayed decision-making and inefficiencies in addressing potential issues
Challenges
The Maintenance teams faced frequent breakdowns due to a reactive maintenance strategy and limited visibility into machine health. Scheduled servicing couldn’t prevent failures, causing delays, higher costs, and poor spare parts planning. Disconnected data and lack of predictive insights hindered early anomaly detection and data-driven decisions, affecting equipment reliability and productivity.
Solution
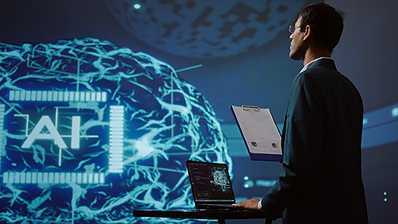
Smart Sensor Integration – Captures real-time machine data on vibration, temperature, pressure and energy usage.
AI-Powered Anomaly Detection – Identifies abnormal machine behavior before failures occur.
Predictive Maintenance Insights – Estimates component lifespan using RUL prediction models.
Instant Alert System – Sends real-time notifications when thresholds are breached.
Centralized Maintenance Dashboard – Visualizes asset health, failure predictions and KPIs.
Deployed Technologies & Integration Approach
Asset Prioritization – Identify critical machines based on risk and downtime impact.
Smart Infrastructure – Set up IoT sensors, edge devices and connectivity.
Data Analysis – Collect and structure historical data and failure logs.
Model Development – Train and validate predictive models for asset behavior.
Pilot Deployment – Test predictions, calibrate thresholds and fine-tune detection.
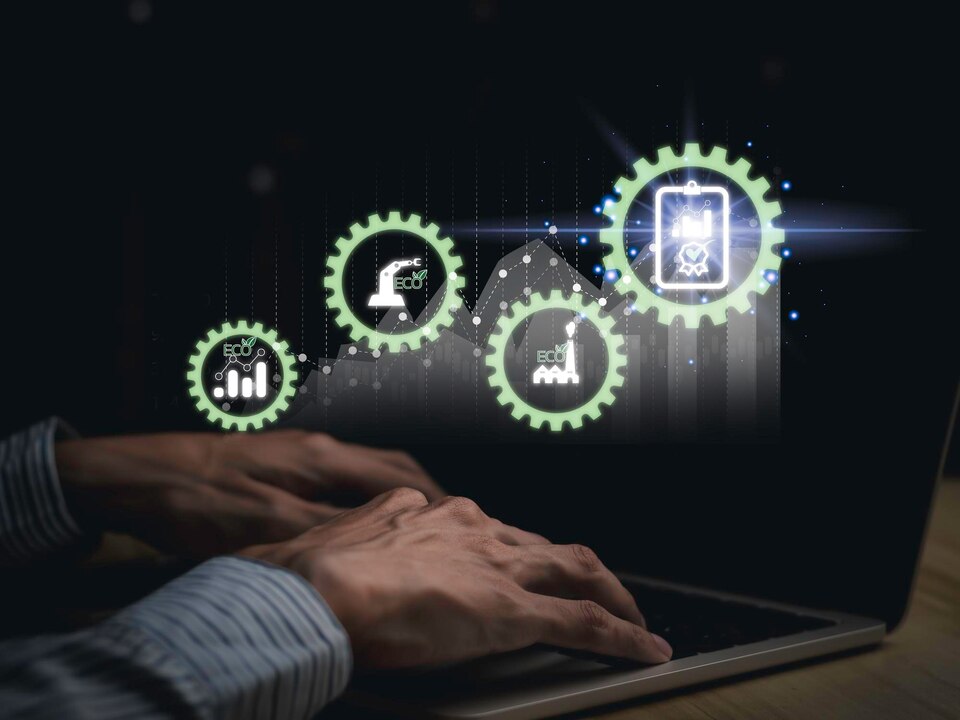
Tangible Results & Business Outcome
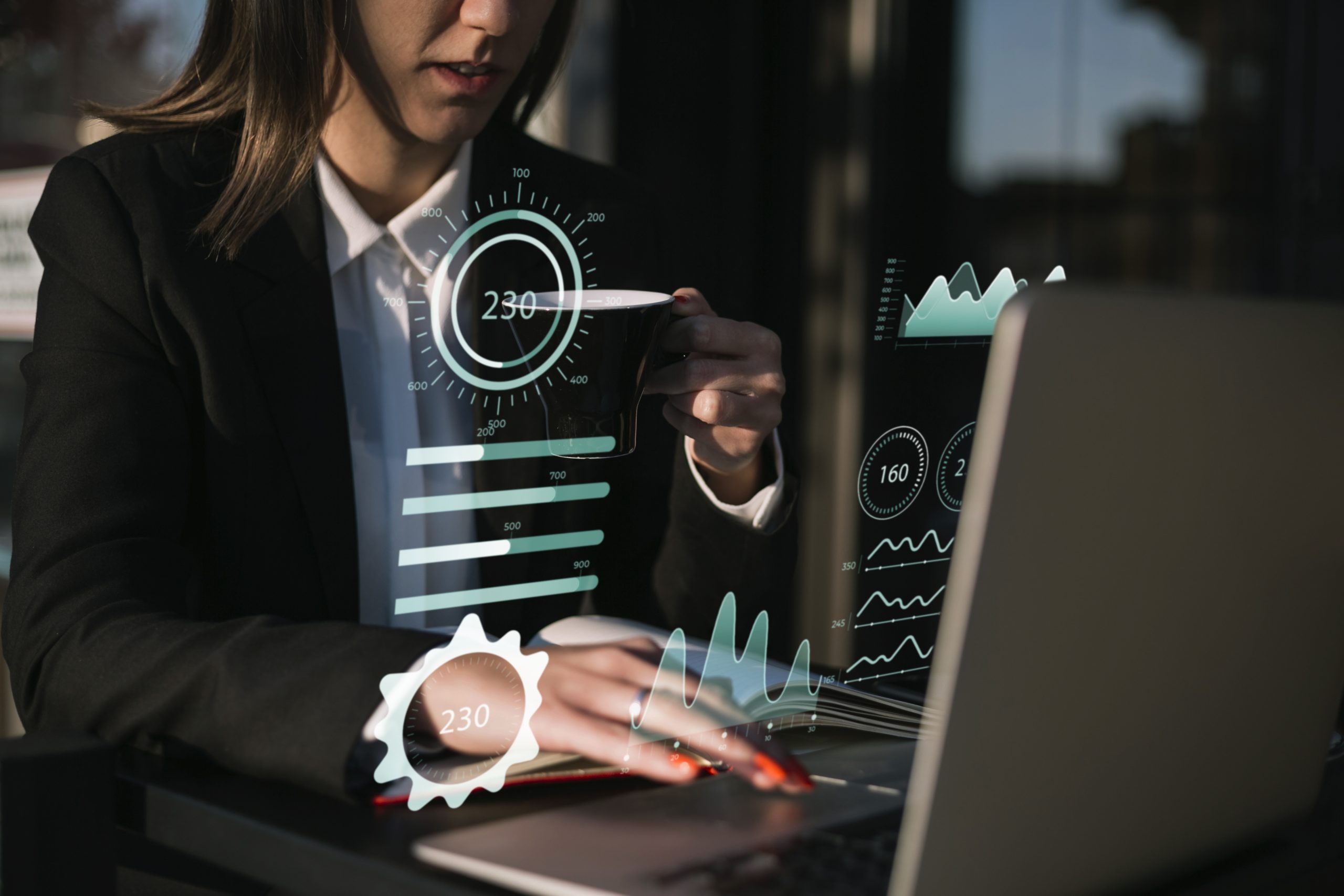
Downtime Reduction: Minimize unplanned equipment failures by up to 50% through predictive maintenance strategies.
Extended Asset Lifespan: Increase the longevity of critical assets with condition-based monitoring and timely interventions.
Cost Optimization: Reduce maintenance-related expenditures by as much as 25% through data-driven maintenance planning.
Proactive Maintenance Planning: Leverage Remaining Useful Life (RUL) predictions to enable smarter scheduling and resource allocation.