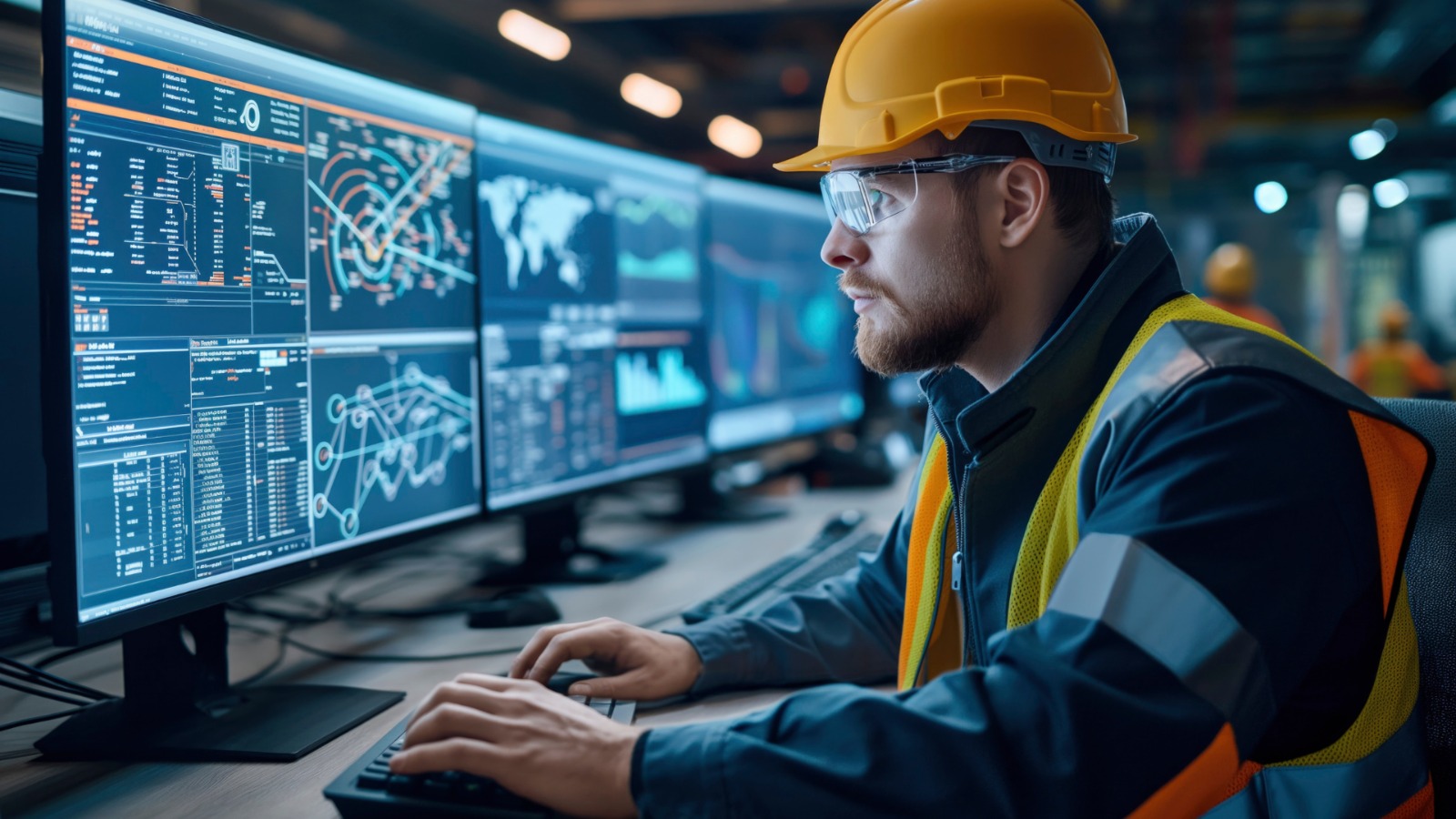
Condition Monitoring
Real-Time Asset Health: Continuously monitor critical machine parameters like vibration, temperature, pressure, etc.
Sensor-Driven Insights: Leverage IoT and edge devices to capture accurate, high-frequency data from key equipment.
Preventive Intelligence: Spot gradual degradation trends and address issues before they escalate into costly failures.